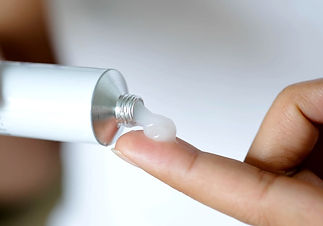
Gel & Ointments Manufacturing
Plant
Topical pain relief medications are applied directly to the skin at the area of inflammation or pain. Topical pain relief products like gels, ointments, and sprays are designed to relieve pain and utilize skin as the vehicle for drug administration. Ointments used for medical purposes contain medications that can either act on the skin or be absorbed through the skin for systemic action.
Common bases for ointments include:
• Petroleum jelly
• Anhydrous lanolin
• Waxes
• Vegetable oils
• Lard
Market Size of Topical Pain Relief Products
The global topical pain relief market size was valued at $8,864.0 million in 2019, and is projected to reach $12,219.7 million by 2027 at a CAGR of 5.2% from 2020 to 2027.
Ingredients used in Ointments Manufacturing
-
Antibiotics
-
Antifungals
-
Corticosteroids
-
Analgesics
-
Antivirals
-
Other APIs
-
Emulsifiers/Thickeners/Stabilizers
-
Base or Vehicles:
-
Petroleum Jelly​
-
White Soft Paraffin
-
Lanolin
-
Oil
-
Water
-
High Shear & High Viscosity Mixing Technology
for Gels & Ointments Manufacturing
High-shear mixers or high-shear homogenizers are used to produce standard mixtures of ingredients that do not naturally mix. This industrial machinery disperses, or transports, one phase or ingredient (liquid, solid, gas) into a main continuous phase (liquid), with which it would normally be immiscible. A rotor, together with a stationary component known as a stator, or an array of rotors and stators, is used in a mixing tank containing the solution to be mixed, and in a pipe through which the solution passes, to create shear. A high-shear homogenizer mixer is used to create emulsions, suspensions, lyosols (gas dispersed in liquid), and granular products. It is used in the food, pharmaceutical, adhesives, chemical, cosmetic, and plastics industries for emulsification, homogenization, particle size reduction, and dispersion.
Key design factors in the high shear mixers include the diameter of the rotor and its rotational speed, the distance between the rotor and the stator.
Ointments Manufacturing Plant & Process
United Group's Ointments Manufacturing Plant uses the high shear and high viscosity mixing technology for production of gels, creams, ointments, lotions, spray solutions and other products related to topical pain relief application.
​
​
Here is a general overview of the typical processing steps:
​
1. Weighing and Measuring Ingredients
2. Mixing Active Ingredients and Base to create a homogenous blend
3. Heating and Melting the ointment base to ensure complete dissolution of the ingredients
4. Incorporation of Active Ingredients, Emulsifiers, Thickeners, Stabilizers
5. Cooling and Homogenization to ensure uniform dispersion and smooth consistency
6. Filling and Packaging

Advantages of United Group's Ointments Plant
United Group's homogenizers rapidly disperse solids into liquids, thereby reducing mixing times and enhancing product uniformity and consistency.
-
Short Batch Times
-
Consistently High Product Quality
-
Excellent Homogenization
-
Rapid Emulsification
-
User-Friendly Operation
-
Used to Manufacture a Wide Range of Product
-
Stirrer and Dispersion Device with Speed Control
-
Prevention of Lump Formation & Clumping
-
Controlled Dosage Rate
-
Suitable for Highest Viscosities
-
Long-time Stability of Emulsions
-
Fine Particle Size Reduction